|
|
|
|
|
|
Expansion
Gaps |
|
|
|
|
|
Expansion
gaps should be placed at intervals determined
by 1) the expansion rate of the metal in the conductor
selected, and 2) the variation in temperature that will
occur at the conductor location over a full year of operation. |
Example:
A 300' long copper conductor system (X)
installed outdoors with an anticipated temperature
fluctuation of 80°F (Y). |
|
Total Expansion
= 300'/100' x 80°F/100°F = 2.4". |
1.
Steel Conductor Systems |
|
3.
Determine the Number of Expansion Gap
Assemblies |
Given
that steel conductors expand 1" for every 150' of
runway with a temperature change of 100°F over a full
year of operation, put the length of the runway and the
maximum temperature change for the system to be used
into the following formula: |
|
After
calculating the actual expansion of the runway
conductor system, use the following rule of thumb to pick
the number of expansion gap assemblies: |
|
a.
Under 1" of expansion, use no expansion assemblies.
Install one anchor clamp set at the center of the
conductor run. |
|
Total Steel Expansion
(inches) = X/150' x Y/100°F |
|
where
X is the runway length and Y is the 12 month
temperature variation. |
|
b.
From 1" to 2" of expansion, use one expansion
assembly in the center of the conductor run. |
Example:
A 450' long steel conductor (X) installed in a
building with an indoor temperature change of 40°F (Y). |
|
c.
From 2" to 4" of expansion, use two expansion
assemblies. Locate them at 1/3 of the runway length in
from each end. |
|
Total Expansion
= 450'/150' x 40°F/100°F = 1.2". |
|
2.
Copper Conductor Systems |
|
d.
For systems with more than 4" of expansion, use one
expansion gap assembly for each 2" of expansion. |
Given
that copper conductors expand 1" for every 100' of
runway over a 100°F temperature change at the conductor
over a full year of operation, put the length of the runway
and the maximum temperature change for the system to
be used into the following formula: |
|
|
4.
Anchors |
|
Anchor
clamps are required at midpoint on all systems
without expansion gaps and halfway between gaps and
from gaps to the end of systems with multiple gaps. See
the Figure 8 Installation Instructions on anchor locations. |
|
Total Copper Expansion
(inches) = X/100' x Y/100°F. |
|
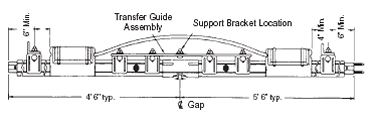 |
|
The
maximum gap opening for all ten foot Figure 8
expansion gap assemblies is 1-3/4 inches. |
|
Expansion
assemblies are also required at building
expansion joints. |
|
|
|